The Future of Industrial Manufacturing: How AI is Revolutionizing Cost Savings and Efficiency
The industrial manufacturing sector stands on the cusp of a technological revolution. As the industry continues to evolve, the integration of Artificial Intelligence (AI) is emerging as a key driver of productivity, efficiency, and cost savings. According to industry reports, the global manufacturing sector is projected to grow at a compound annual growth rate (CAGR) of 4% from 2020 to 2025. This growth is significantly bolstered by the increasing adoption of AI, which is transforming traditional manufacturing processes into smart, efficient systems.
AI in Industrial Manufacturing: The Key to Unlocking $3.27 Trillion in Savings
AI’s potential in industrial manufacturing is immense, offering companies the ability to predict equipment failures, optimize operations, and enhance quality control. These advancements translate into substantial cost savings, with the potential to save the global manufacturing industry approximately $3.27 trillion. Companies like Lincoln Electric, Parker Hannifin, and Graco Inc. are already leveraging AI to achieve significant savings through predictive maintenance, quality control, and supply chain optimization.
How AI Drives Cost Savings in Manufacturing
AI’s impact on industrial manufacturing can be broken down into several key areas:
- Predictive Maintenance:
Predictive maintenance powered by AI enables companies to foresee equipment failures before they happen. By analyzing data from various sensors and systems, AI can predict when a piece of machinery is likely to fail, allowing for proactive maintenance. This reduces downtime and minimizes repair costs. For example, Lincoln Electric has been able to reduce annual downtime costs by $60 million through AI-driven predictive maintenance. - Operational Optimization:
AI analyzes vast amounts of data from manufacturing processes to identify inefficiencies and suggest improvements. This leads to optimized operations, improved productivity, and reduced operational costs. Parker Hannifin, for instance, has realized annual savings of $300 million by leveraging AI to streamline its manufacturing processes. - Quality Control:
AI-driven quality inspection systems are capable of detecting defects in real-time. By identifying issues during the manufacturing process, these systems help reduce waste and improve product quality. Graco Inc. has implemented AI-powered quality control measures, resulting in a reduction of downtime costs by $40 million annually.
Case Studies: AI Implementation in Leading Industrial Manufacturing Companies
Lincoln Electric: Maximizing Uptime with AI-Powered Predictive Maintenance
Lincoln Electric, a global leader in industrial manufacturing, has embraced AI to enhance its predictive maintenance capabilities. By integrating AI into its maintenance processes, the company has reduced downtime costs by 20%, saving approximately $60 million annually. This proactive approach to maintenance not only minimizes unplanned downtime but also extends the lifespan of critical equipment. Learn more about how AI is changing this industry by visiting here.
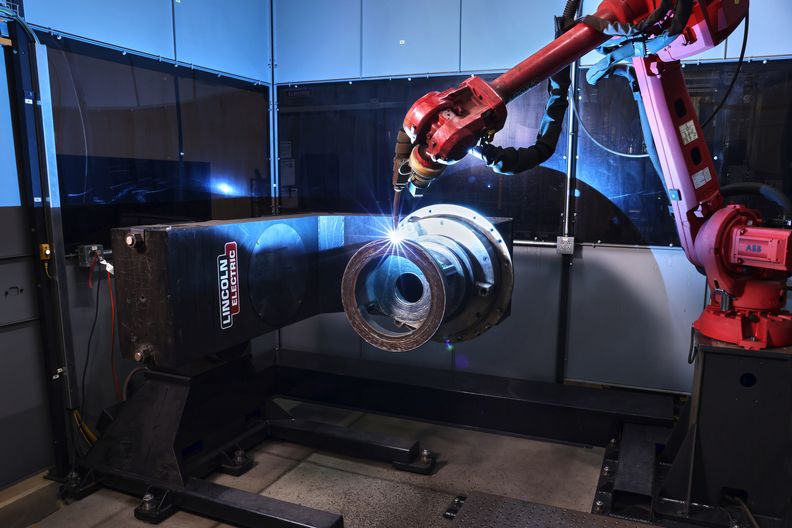
Parker Hannifin: Streamlining Operations for Cost Efficiency
Parker Hannifin, a leader in motion and control technologies, has harnessed the power of AI to optimize its manufacturing operations. By analyzing data from its production lines, AI has helped the company identify bottlenecks and inefficiencies, leading to operational improvements and annual savings of $300 million. This has been a game-changer for Parker Hannifin, significantly boosting its overall efficiency.
Graco Inc.: Enhancing Quality Control with AI
Graco Inc., a prominent manufacturer of fluid handling systems, has utilized AI to improve its quality control processes. AI-powered inspection systems detect defects in real-time, allowing the company to address issues immediately and reduce waste. This implementation has resulted in an annual savings of $40 million in downtime costs.
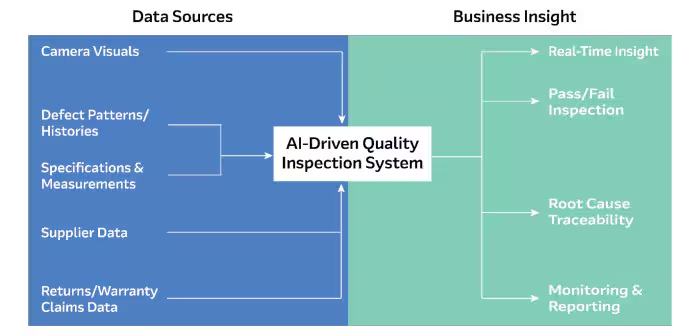
The Broader Impact: AI-Driven Savings Across the Industrial Manufacturing Sector
The examples of Lincoln Electric, Parker Hannifin, and Graco Inc. are just a few illustrations of how AI is transforming industrial manufacturing. When scaled across the industry, the potential savings are staggering. Here’s a closer look at the impact AI could have on other major players in the sector:
- SPX Corporation:
By integrating AI into its operations, SPX Corporation has the potential to reduce downtime costs by 15%, saving approximately $240 million annually. Furthermore, AI-driven supply chain optimization could save the company an additional $240 million per year. - Nordson Corporation:
AI is expected to save Nordson Corporation around $735 million annually by predicting equipment failures and enhancing quality control processes. This represents a 15% reduction in downtime costs and a 20% reduction in defects and waste. - IDEX Corporation:
With AI, IDEX Corporation could reduce downtime costs by 15%, saving around $375 million annually. Additionally, AI could optimize supply chain operations, yielding another $375 million in savings. - Milacron:
For Milacron, AI-driven predictive maintenance and quality control could result in savings of $165 million and $220 million annually, respectively. - Regal Beloit:
Regal Beloit could save approximately $435 million annually by reducing downtime costs through AI. Another $435 million could be saved through AI-enabled supply chain optimization. - ITT Inc.:
AI implementation at ITT Inc. could result in $875 million in annual savings, with $375 million coming from reduced downtime costs and $500 million from enhanced quality control processes.
AI’s Role in the Future of Industrial Manufacturing
The integration of AI in industrial manufacturing is not just a trend; it’s the future. As the industry continues to grow, companies that embrace AI will have a competitive edge. The potential for cost savings, increased efficiency, and enhanced product quality is driving more and more manufacturers to invest in AI technologies.
However, the journey towards full AI integration is not without challenges. Companies must navigate issues such as data security, the need for skilled personnel, and the initial investment required for AI adoption. Despite these hurdles, the long-term benefits far outweigh the costs.
Conclusion: The Road Ahead for AI in Manufacturing
The industrial manufacturing sector is poised for a transformation, with AI leading the way. The potential savings of $3.27 trillion globally highlight the significant impact that AI can have on the industry. Companies like Lincoln Electric, Parker Hannifin, and Graco Inc. are already reaping the benefits of AI, and as more manufacturers follow suit, the industry will continue to evolve.
For those in the industrial manufacturing sector, the message is clear: embracing AI is no longer optional—it’s essential. The future of manufacturing lies in AI-driven technologies that enhance productivity, reduce costs, and improve quality. As we look ahead, the companies that invest in AI today will be the ones leading the industry tomorrow.
Find other related articles about how AI is changing our business environment by visiting here.